قطعی برق چه بر سر فولاد خوزستان آورد؟
فولادسازان در تاریکی/ کورههای خاموش «فخوز»
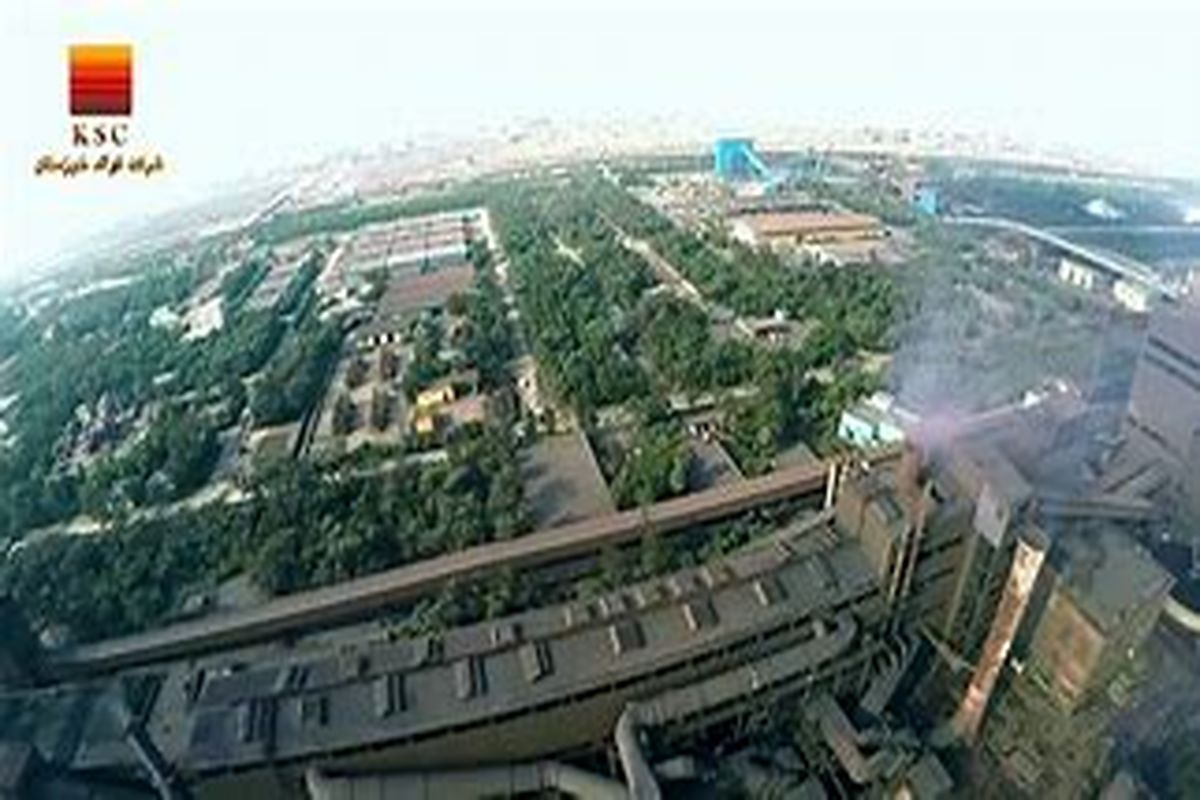
به گزارش خبرنگار حوزه صنعت اولین خبر: شرکت فولاد خوزستان، یکی از بزرگترین تولیدکنندگان فولاد در ایران، بهعنوان یک شرکت صنعتی بزرگ در اقتصاد کشور نقش مهمی ایفا میکند. در سالهای اخیر، این شرکت با مشکلاتی از جمله قطعیهای مکرر برق مواجه شده است که تأثیرات گستردهای بر تولید، اقتصاد و بهرهوری این شرکت داشته است.
هر ساله و با آغاز فصل تابستان صنایع با قطعی برق مواجه میشوند؛ قطعی برق و هزینه انرژی همیشه دو چالش بزرگ برای شرکتهای فولادی بوده است. اینکه شرکتها هزینههای گزافی برای انرژی پرداخت میکنند و از طرفی با کمبود انرژی هم مواجه میشوند، جزو چالشهای بزرگی است که شرکت را با مشکلات متعددی روبهرو میکند.
صنعت فولاد یکی از مهمترین صنایع در کشور ما است که نقش کلیدی در توسعه اقتصادی و صنعتی کشور ایفا میکند. تولید فولاد یک فرایند انرژیبر است که به مصرف بالای انرژی نیاز دارد. هزینههای انرژی سهم بزرگی از هزینههای عملیاتی شرکتهای فولادی را تشکیل میدهد. در کشور ما، به دلیل عوامل متعددی، این هزینهها بهویژه برای شرکتهای فولادی افزایش یافته است. این صنعت بهشدت به برق وابسته است، زیرا فرایندهای تولید فولاد نیاز به انرژی فراوان دارند. در سالهای اخیر، قطعیهای برق مکرر و گسترده در ایران، بهویژه در فصل تابستان، به چالشی بزرگ برای این شرکتها تبدیل شده است.
در این گزارش به بررسی علل هزینهی بالای انرژی، بررسی پیامدها و واکنشهای مختلف به قطعی برق شرکت فولاد خوزستان پرداخته خواهد شد.
علل هزینهی بالای انرژی در شرکتهای فولادی ایران
فرسودگی و کارایی پایین تجهیزات
بسیاری از کارخانههای فولادی در ایران از تجهیزات و ماشینآلات قدیمی و فرسوده استفاده میکنند. این تجهیزات نهتنها بهرهوری انرژی کمتری دارند؛ بلکه هزینههای تعمیر و نگهداری بالایی نیز به همراه دارند. فرسودگی تجهیزات منجر به مصرف بیشتر انرژی و افزایش هزینههای مربوط به آن میشود.
قیمتگذاری نامناسب حاملهای انرژی
در ایران، قیمتگذاری حاملهای انرژی همچون گاز طبیعی و برق به طور مستقیم توسط دولت تعیین میشود. در سالهای اخیر، با افزایش قیمت جهانی انرژی و همچنین اصلاحات تدریجی در یارانههای انرژی، هزینه انرژی برای صنایع مختلف از جمله صنعت فولاد افزایش یافته است. این افزایش قیمتها تأثیر مستقیمی بر هزینههای تولید شرکتهای فولادی دارد.
وابستگی به منابع انرژی فسیلی
بخش عمدهای از انرژی مورد نیاز صنایع فولادی در ایران از منابع انرژی فسیلی تأمین میشود. قیمت این منابع به دلایل مختلف از جمله نوسانات بازار جهانی نفت و گاز و تغییرات سیاستهای داخلی و بینالمللی قابلتغییر است. افزایش قیمت جهانی نفت و گاز طبیعی به طور مستقیم منجر به افزایش هزینههای انرژی برای شرکتهای فولادی میشود.
کمبود و قطعیهای مکرر انرژی
به دلیل تقاضای بالای انرژی و ظرفیت محدود تولید و انتقال برق و گاز، شرکتهای فولادی ایران با کمبود و قطعیهای مکرر انرژی مواجه هستند. این قطعیها میتواند منجر به توقفهای مکرر در تولید، کاهش بهرهوری و در نتیجه افزایش هزینههای عملیاتی شود. شرکتها معمولاً مجبورند برای مقابله با این قطعیها، به استفاده از منابع انرژی جایگزین و گرانتر مانند ژنراتورهای دیزلی روی آورند.
راندمان پایین فرایندهای تولید
فرایندهای تولید فولاد در ایران به دلایل مختلفی از جمله فناوریهای قدیمی و ناکارآمد، مدیریت نامناسب منابع و عدم استفاده بهینه از انرژی، راندمان پایینتری نسبت به استانداردهای جهانی دارند. راندمان پایین منجر به مصرف بیشتر انرژی برای تولید هر تن فولاد میشود که این امر هزینههای انرژی را افزایش میدهد.
پیامدهای هزینهی بالای انرژی برای شرکتهای فولادی ایران
افزایش هزینههای تولید
هزینههای بالای انرژی به طور مستقیم باعث افزایش هزینههای تولید در شرکتهای فولادی میشود. این افزایش هزینهها میتواند حاشیه سود شرکتها را کاهش دهد و توان رقابتی آنها را در بازارهای داخلی و بینالمللی تحتتأثیر قرار دهد. در شرایطی که بازار جهانی فولاد بهشدت رقابتی است، افزایش هزینههای تولید میتواند منجر به ازدستدادن سهم بازار شود.
کاهش توان سرمایهگذاری و توسعه
با افزایش هزینههای انرژی، منابع مالی کمتری برای سرمایهگذاری در بهبود و توسعه فناوریها و فرایندهای تولید باقی میماند. این امر میتواند منجر به کاهش توان شرکتها در بهروزرسانی تجهیزات، بهبود راندمان انرژی و کاهش هزینههای عملیاتی شود.
تأثیرات منفی بر محیطزیست
مصرف بالای انرژی و استفاده از سوختهای فسیلی در فرایندهای تولید فولاد منجر به تولید میزان زیادی از گازهای گلخانهای و آلودگی هوا میشود. هزینههای بالای انرژی میتواند شرکتها را از سرمایهگذاری در فناوریهای پاکتر و کارآمدتر باز دارد و در نتیجه، تأثیرات منفی بر محیطزیست افزایش یابد.